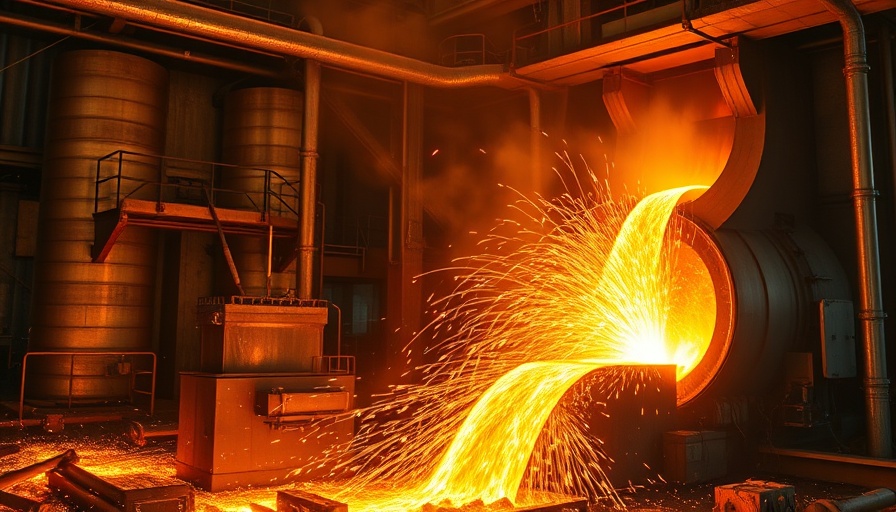
Boston Metal’s Groundbreaking Steelmaking Technology
Boston Metal, a startup founded on revolutionary research from MIT, has taken a significant step in the quest for sustainable steel production. Their latest achievement, successfully running the largest reactor to date, produced over a ton of steel using a method called molten oxide electrolysis (MOE). Unlike traditional steelmaking that relies on coal-based coke, this process utilizes electricity to eliminate carbon emissions associated with steel production.
Understanding the Significance of Green Steel
Steel is responsible for nearly 8% of global carbon emissions, and the industry's reliance on fossil fuels makes its decarbonization a complex challenge. The promise of Boston Metal's technology lies in its ability to address not just emissions, but also the enormous demand for steel, which exceeds 2 billion metric tons annually. Through MOE, Boston Metal can convert iron ore directly into molten metal without producing CO2, thus marking a pivotal advancement towards achieving net-zero steelmaking.
Electrolysis: A Game-Changer for the Steel Industry
The process developed at Boston Metal involves heating iron ore to over 2,900 degrees Fahrenheit while passing an electric current through it. This causes the oxygen in the ore to separate, emitting pure oxygen instead of harmful greenhouse gases. This innovative technique draws inspiration from other sectors looking for sustainable solutions, aligning the steel industry with global ecological goals.
Challenges and Future Directions
Despite the breakthrough, challenges remain. One of the key components—anodes used to conduct electricity—can degrade over time, potentially affecting production efficiency. Boston Metal is currently addressing these issues by enhancing anode durability while scaling up their reactor’s size and output. Looking ahead, they aim to enhance production capacity to deliver a ton of steel daily by the end of 2027, positioning themselves as leaders in the green steel market.
The Broader Impact of Green Steel Technology
The implications of Boston Metal's achievements extend beyond the factory floor. By prioritizing clean energy strategies in steel production, they represent a significant leap towards industrial decarbonization—a crucial factor in mitigating climate change. Their technology could revolutionize metal manufacturing while supporting economic growth and environmental stewardship.
As this technology develops, it offers valuable insights for industries worldwide seeking to modernize their operations sustainably. Monitoring these advancements will be essential for investors, educating them on potential opportunities while inspiring other manufacturers to explore cleaner processes.
For those interested in climate innovation, staying updated on Boston Metal’s progress is vital. The environmental stakes are high, making each step towards a greener steel industry a collective win for our planet.
Write A Comment